Newport NC Heating Air & Conditioning Services
Jackson and Son specializes in professional, 100% guaranteed residential and commercial heating and air conditioning installation, maintenance tune-ups and repair services.
Read what your Newport, NC neighbors say about our quality services, then call us at 919-734-9611 to schedule an appointment.
Local Reviews
for Newport, NC
Customers say: The recent reviews exhibit a positive overall sentiment, with a slight inclination towards the positive. The reviewers express satisfaction with the services provided, highlighting the helpfulness, expertise, and professionalism of the technicians. They mention the timeliness, efficiency, and quality of the work done. Additionally, the reviewers appreciate the courteous and respectful behavior of the technicians, as well as their willingness to answer questions and provide detailed explanations. The positive reviews also mention the positive experiences with the company's customer service, including the ease of scheduling appointments, the clarity of the pricing, and the overall positive impression left by the technicians. However, it's worth noting that the negative reviews are fewer in number and do not contain any significant negative sentiment. Overall, the reviews suggest that customers have had positive experiences with Jackson and Sons and would recommend their services to others.
Our Reviews by City
Lots of work on this property. Great service!
PRIME - Newport, NC 28570
With 9+ HVAC systems, there's a lot of work to maintenance the property's equipment. He kept me in the loop through out
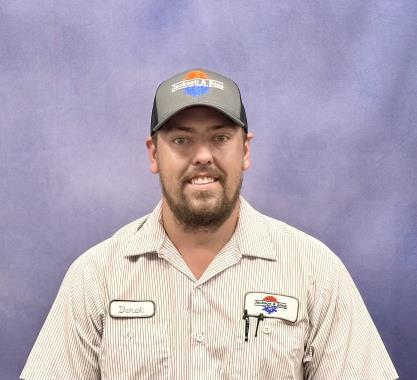
Derek J.
Upon arrival tech was informed system for office was running continuously and blowing hot air. Inspected system and found the relay on the blower control board was shorted causing the blower to engage which also caused the heat strips to come on. Installed a new relay in air handler and tested heat and cooling operation and system is back operational. System is not cooling the best, it is a R22 Freon. Recommends replacing system due to age and Freon type.

Kyle W.
Performed ESA on (1) Mitsubishi Mini Split system. All (3) zones working properly at this time. Cleaned all filters/coils, cleared drain lines, and re-secured line-set covers shown in pictures.
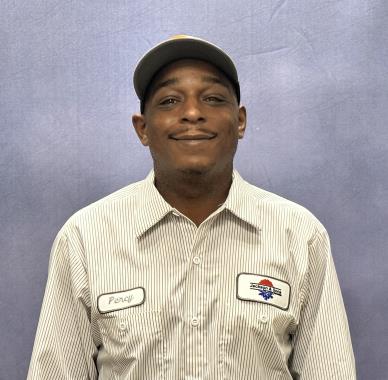
Percy M.
PERFORMED CMA INSPECTION ON 9 SPLIT SYSTEMS AND 1 DEHUMIDIFIER. SPLIT SYSTEM BG-J AIR HANDLER SYSTEMS EVAPORATOR COIL HAS A LARGE AMOUNT OF RUST ON COIL, SYSTEM WAS INSTALLED IN 2003 AND IS 21 YEAR OLD, TECH RECOMMENDS REPLACEMENT OF SYSTEM. SPLIT SYSTEM BG-J CONDENSER UNIT IS NOT LEVEL. RECOMMEND LEVELING SYSTEM TO ENSURE PROPER OPERATION OF SYSTEM, THERE IS AN ESTIMATE PROVIDED FOR LEVELING OF SPLIT SYSTEM BG-J. ALL SYSTEMS ARE PERFORMING PROPERLY AT THIS TIME. TECH CHANGED FILTERS AND FLUSHED ALL DRAIN LINES.
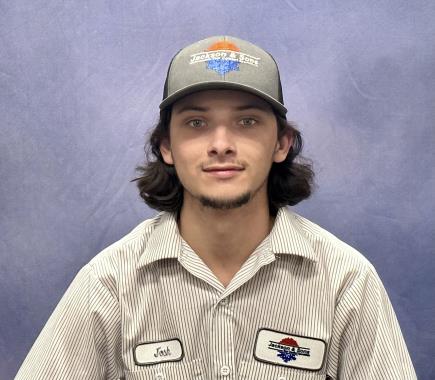
Josh W.
Tech performed esa on one system, system is only 5 months old and in excellent condition, tech did not find any challenges at this time. System is back on and operating properly at this time.
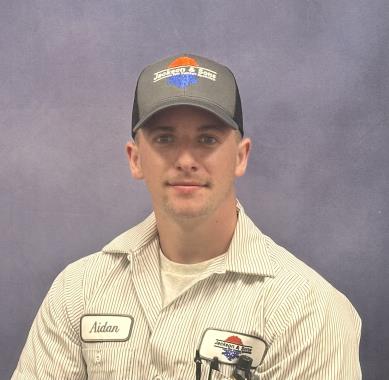
Aidan T.
- Customer informed tech that the crawl space has excessive moisture, despite 4 dehumidifiers and 2 pumps. - Customer informed tech that their crawl space encapsulation contractor is scheduled to visit next week. - Tech informed customer of all these issues and recommended course of action. Tech examined crawlspace and discovered the following: 1. Trunk line and numerous flex supply ducts are resting on the ground. The insulation and jackets are saturated and should be replaced. 2. Line sets are not insulated and are contributing to moisture issue. Checked drain lines and flushed/vacuumed both drains. 3. PVC drain outlets discharge water onto a downward slope, pushing the water back into the foundation of the home. 4. Dehumidifiers do not seem to function correctly. Course of action: 1. Hire landscaper to install a perforated drain system to direct drain discharge away from home or re-grading slope away from the home. 2. Hire crawl space contractor to remove current standing water

Caleb S.
Spoke with customer over the phone about repair vs. replace. He is going to speak with his wife and contact us back.
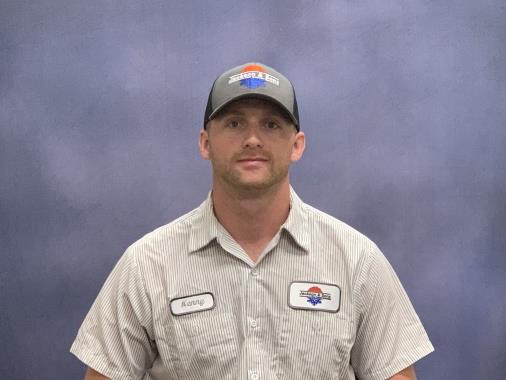
Kenny C.
Performed ESA, tech found leak in evaporator coil. Coil was also caked up and covered in nicotine. Tech cleaned off coil and informed homeowner of findings. Homeowner stated her uncle is the one that set up today’s visit and to contact him. Field supervisor is to contact the customer to inform him of his options.

Dalton B.
UNIT #1 (300 WING)-4 TON TRANE SPLIT HEAT PUMP

Dalton B.
UNIT #8 (DINING ROOM)- 3 TON TRANE SPLIT SYSTEM HEAT PUMP
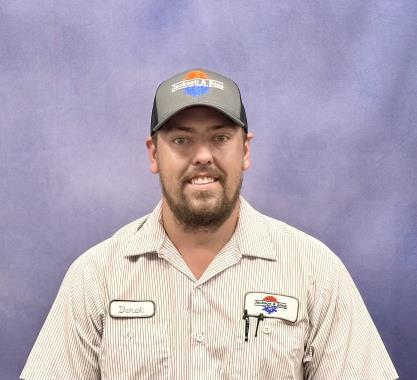
Derek J.
Upon inspection on System #6 tech confirmed leak at evaporator coil on 2 year old system and will need to order new coil. System #7 has 215v coming into unit and 24v coming out of transformer but is not coming back through alarm relay. Alarm company needs to replace relay to get unit back running.

Dalton B.
LINESET REPLACEMENT
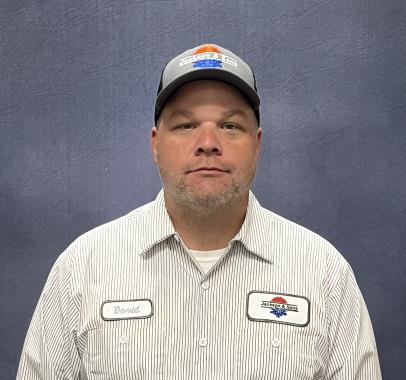
David S.
Dropped off reserve tank of nitrogen. Left 01451 filter dryer.
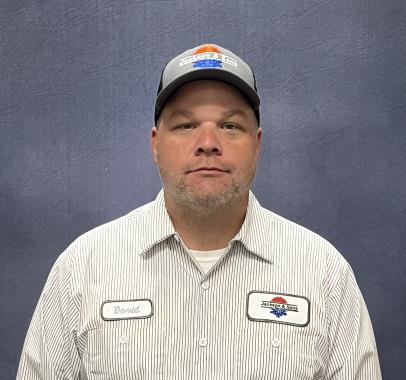
David S.
-Installed EZ Trap on Air Handler 3 & 4 per prior approval. Insulated trap with insulating tape, cleared drain lines with compressed nitrogen. -Replaced 7.5 mfd outdoor fan motor capacitor on HP-4 per prior approval. Observed no status light at heat pump control board. Verified no voltage at heat pump by jumping Y and R circuit. Verified air handler disconnect in on position. System is likely in need of demand tech to diagnose. Thermostat is not blank but shows low battery warning.
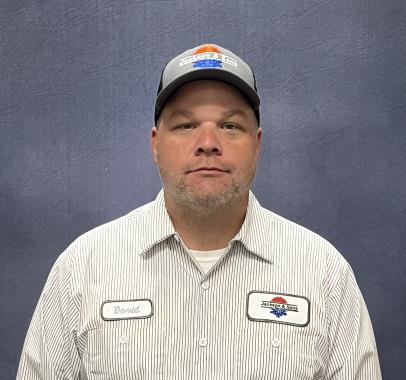
David S.
-Performed CMA Full Service on 9 Split System Heat Pumps and 1 Dehumidifier. -Office Building System: Compressor side of dual run capacitor tested very weak. No room to add additional capacitor, recommend replacement of dual run capacitor. System is over 20 yr old R22 refrigerant. Customer should consider replacing system. -Building H: Dehumidifier run into existing drain line. Vent on wrong side of trap. Recommend adding EZ Trap to properly vent and service drain line. -Building J: Blower motor capacitor tested weak. Recommend replacement of capacitor. Outdoor fan motor hot to the touch. Compressor megged as caution. Windings deteriorating and due for shorting/failure. Signs of heat damage at condenser unit wiring. Temperature difference in cooling not as expected. Air handler approximately 20 yr old. Condenser approximately 30 yr old. R22. Replacement of system is recommended. -Building L: Compresso
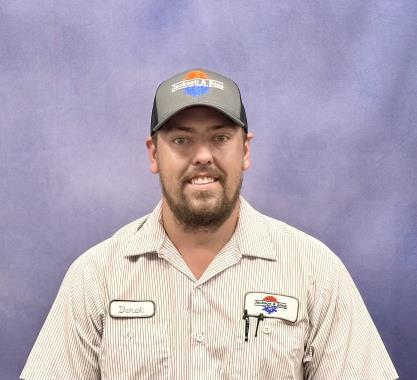
Derek J.
Upon arrival tech began inspecting GP #2 and found Circuit 2 contact had 2 burnt wires due to loose connections causing the contactor to fail. Tech replaced 3 phase contactor and Circuit 2 began working. Compressor amps and pressures were within range. System back operating at this time.
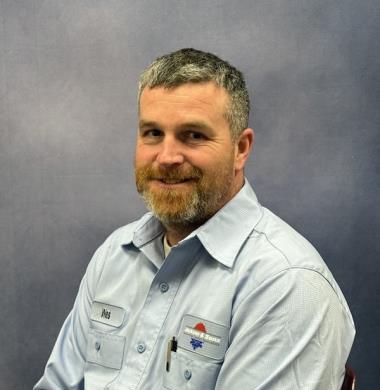
Wes B.
Performed routine maintenance per CMA agreement. 3 gas package units- Full Service on Kitchen, Inspections on 2 Dining Room Units, 2 Make Up Air Units, 1 DOAS system, 6 exhaust fans Challenges present - GP 2, upon starting the inspection, the technician observed circuit 2 was being called for, however, the compressor was not running. Technician shut off system, waited a few minutes and then restored power. Circuit 1 came on as normal. When circuit 2 was called for, the compressor amped to around 44, then went back to 0. Technician checked compressor to ground and got OL. GP 2 - on circuit 1 initially it was cooling properly, with a 18 degree delta t. During inspection, technician heard the reversing valve, seem to de-energize. Tech checked delta t and found it to be 0 as if system was not cooling. System continued running and then after about 10 minutes, the same noise was present and the system started to cool again. Tech assessed electrical connects and everything appears to be co
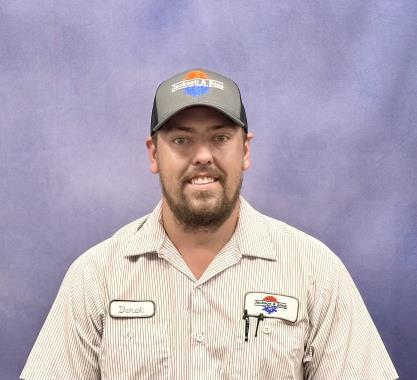
Derek J.
Tech inspected mini split and ran all 3 zones in heat and cooling. Ran each zone individually in heat and cool. ohmed eev’s, thermistors and checked all components on system and everything read within range. Tech reached out to LG tech support and they suggested it has a potential leak in the unit. Tech added 2lbs and 8oz of R410A to system to get them by for now and wanted us to return sometime next week to perform level 4 leak search and figure out exactly where the leak could be located. Homeowner gave tech key card for gate access and showed where key for house is located at. Tech returned to perform leak search. Leaks were found at the master bedroom evaporator coil and flare connections. The living room evaporator coil and flare connections. The loft bedroom flare connections. And the suction line for Circuit A at condenser. Tech recovered 3lbs of Freon with factory charge being 4lbs. Pressure tested with nitrogen and soap bubbles all flares and made repair at Circuit A suction a
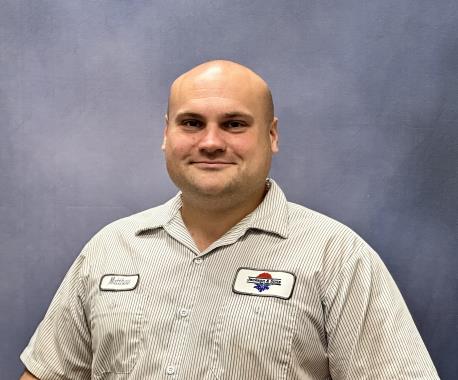
Matthew L.
Unit is 5 years old. Customer was wanting ballpark to replace multizone mini split (1 condenser with 3 heads) gave ballpark over the phone. Customer will think about it and let us know.
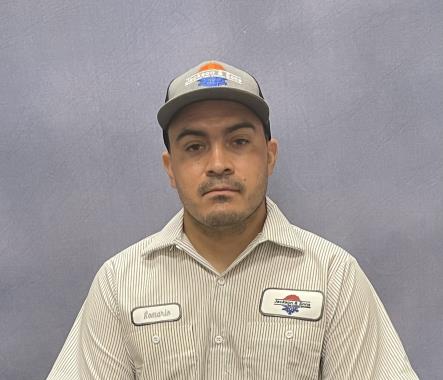
Romario T.
Tech found no trouble codes on display at the condenser unit or the airhandlers. Compressor did not seem to be operating, system had standing pressures. Tech opened up the compartment for the compressor and checked for ohm values and compared it to LG standards, which checked out okay. Tech cycled the power to reset the system and tested all 3 airhandler heads and it appeared to operate properly. Tech did catch the middle port starting to build up frost but went away after 10 seconds. Stepper motors of EEVs are operating properly, normal range of refrigerant levels were found. Tech turned off the mini split from the control thermostats and started them up in cool twice and system started up without challenges, Costumer has had multiple challenges in the past with this LG multi head mini split every year and is wanting a permanent solution, meaning replacing it with a Mitsubishi brand. Field supervisor will be notified and will provide a solution to the homeowner. Costumer requested to

Bryce C.
Spoke with customer over the phone customer no longer wanted appointment said the single wide was not worth investing in new package system
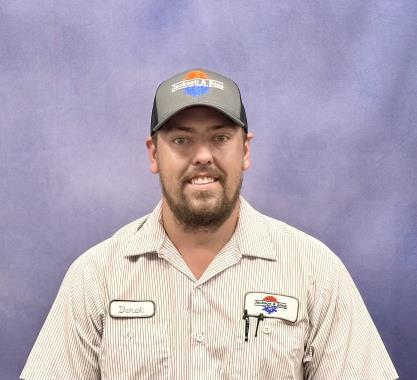
Derek J.
Upon arrival tech was told 3 zone mini split was not cooling. Tech leak searched condenser coil and 3 evaporator coils and found no leaks. Searched all flare fitting outside with no leaks found. Tech believes one leak is located behind wall were the flare joint was cut and brazed together. Homeowner only wanted to clean filters and 1 blower wheel due to potentially wanting to replace everything. Tech installed leak freeze and 3.5lbs of R410A to get unit running for the time being.
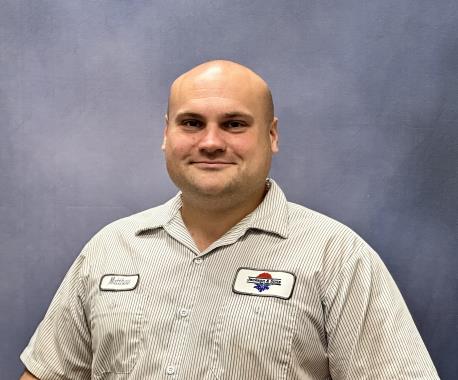
Matthew L.
Customer is going to see how long unit will last until replacing. Did not leave quote at this time.
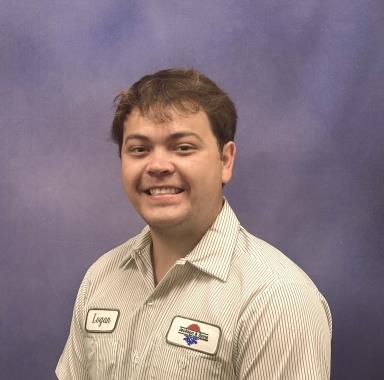
Logan P.
Tech washed and serviced unit and found no challenges at this time. Tech put key back where it was under the condenser.
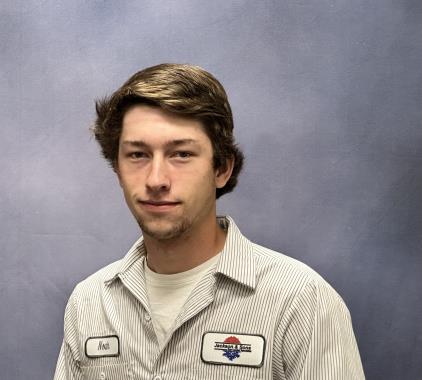
Noah C.
Performed CMA filter change. Tech replaced and disposed of all existing air filters. Also washed make up air unit filters, photos on file.
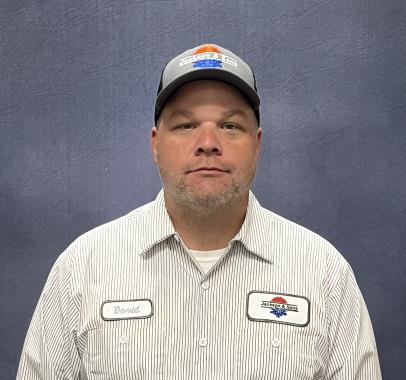
David S.
-Performed CMA Inspection on 11 split system heat pumps. -Split System 1: Compressor failed megohm test at last maintenance. Windings shorting and compressor likely due for failure. Compressor contactor dark and pitted. Recommend replacement of contactor. 2 pole 30 A. Provided estimate $270.23. Outdoor fan motor amperage slightly high. Outdoor fan motor capacitor tested weak. Recommend replacement of capacitor. Provided estimate $209.77. Observed melted connection at air handler high voltage wiring. Recommend installing split bolts at high voltage wires (3 phase). Provided estimate $172.41. Recommend rewire of heat strips using contactors. Further diagnosis of heat strips should be performed upon approval of wiring repair. System has been recommended for replacement. System should be left off at air handler until wiring repairs may be made or system replaced. -Split System 2: Found proper low voltage on R circuit coming from transformer. Circuit runs to fire alarm junction box then b