Raleigh NC Heating Air & Conditioning Services
Jackson and Sons has been serving the heating and air conditioning needs of Raleigh, NC residents and businesses since 1974.
Our reviews below from your neighbors in Raleigh, NC tell the story of our quality, dedication and commitment to customer service.
Local Reviews
for Raleigh, NC
Customers say: The recent reviews exhibit a positive overall sentiment, with a slight inclination towards the positive. The reviewers express satisfaction with the services provided, highlighting the helpfulness, expertise, and professionalism of the technicians. They mention the timeliness, efficiency, and quality of the work done. Additionally, the reviewers appreciate the courteous and respectful behavior of the technicians, as well as their willingness to answer questions and provide detailed explanations. The positive reviews also mention the positive experiences with the company's customer service, including the ease of scheduling appointments, the clarity of the pricing, and the overall positive impression left by the technicians. However, it's worth noting that the negative reviews are fewer in number and do not contain any significant negative sentiment. Overall, the reviews suggest that customers have had positive experiences with Jackson and Sons and would recommend their services to others.
Our Reviews by City
Friendly and knowledgeable tech
Millient - Raleigh, NC 27607
Bryce went out of his way to be helpful, thorough and friendly.
Millicent - Raleigh, NC 27607
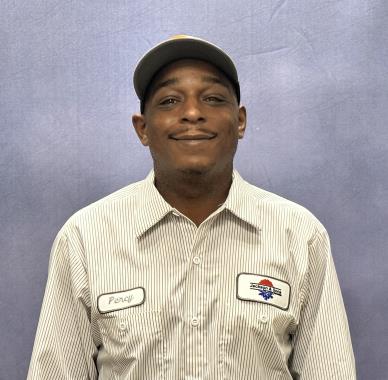
Percy M.
PERFORMED CMA INSPECTION ON 6 GAS PACKAGE SYSTEMS AND 2 MAKE UP AIR SYSTEMS. GAS PACKAGE #5 WASHABLE FILTER (16x30x1) HAS TORN APART AND IS IN BAD CONDITION. TECH RECOMMENDS REPLACEMENT OF FILTER, THERE IS AN ESTIMATE FOR REPLACEMENT OF FILTER ATTACHED TO THIS INVOICE.ALL STSEMS ARE PERFORMING PROPERLY AT HTHIS TIME. THERE ARE PICTURES AND A PERFORMANCE REPORT ATTACHED TO THIS INVOICE.
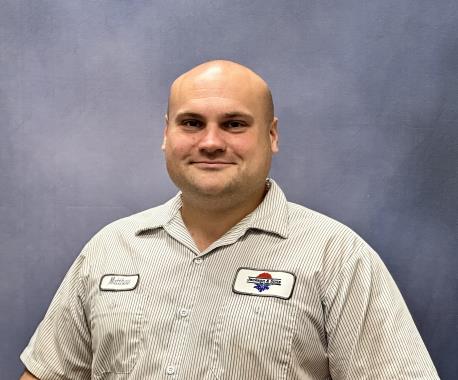
Matthew L.
Mini split starts up after time delay and runs for only a few seconds before shutting down with a 5 flash at indoor unit. 5 flash according to mylinkdrive troubleshooting refers to outdoor power system. Indoor unit manual reports that condition causes compressor to stop for overcurrent protection or start up failure protection. As tech saw outdoor unit shut down, tech gets a 2 red flash at outdoor unit control board. Tech also found a wire rub on the white wire leading to compressor. Tech repaired wire rub with wire nut. Compressor ohms fine with fieldpiece meter, but pressure tap pressure does not change when outdoor fan starts. Compressor is not starting. Tech got DC line voltage on white and red lead on one occasion. Tech got no voltage on each subsequent try. Tech suspects faulty outdoor unit control board due to wire rub. Tech recommends ordering outdoor unit board and also installing a surge protector. Outdoor unit serial number is correct in ServiceTitan (last four are 2875). C
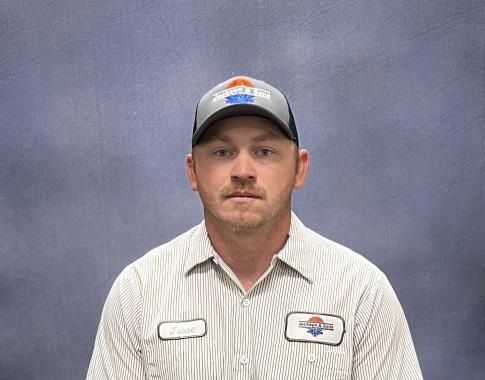
Jesse J.
Replace 2.5 Ton Package Heat Pump With New Mitsubishi 2.5 Ton Mini Split Heat Pump With WiFi Programmable Thermostat

Jerry H.
Pre smoked 10 ton unit and it passed. 10 ton, unit 427, unit 429, and unit for bathrooms all passed electrical and mechanical inspection. Sealed up line set penetration on roof for 10 ton unit per inspectors recommendation. Sent pic to inspector after sealing.

Amber W.
Inspector noted more needs done. Smaller gauge for pressure test, gas lines need repainted for better coverage, audible and visual alarms needs wired in for duct detector, door needs put on split system for filter access. Gas line inside is good with the stickers I put on.

Dalton B.
Hung branch lines tied in gas line
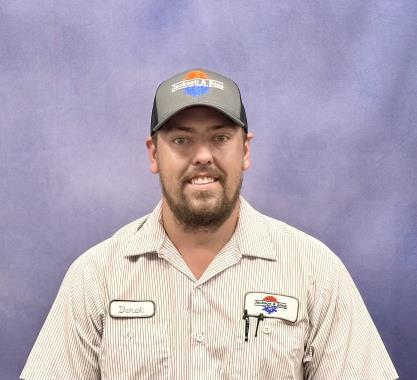
Derek J.
Tech changed out Symbio board on new Trane gas pack and system still had same issues. After speaking with office we will return to further inspect. Tech installed original Symbio board back on system.
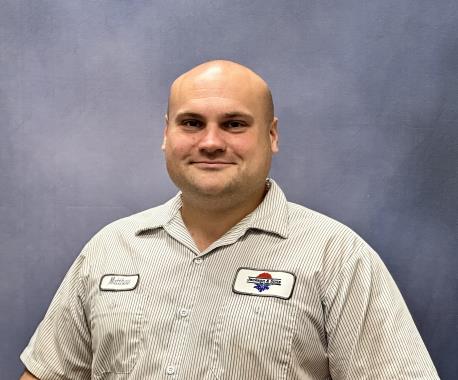
Matthew L.
On arrival no power to system. WEC here and got corrected…..fuse blown in main panel. Cannot get system to turn on. Surge that hit fuse may have damaged something in system. Need to return with duct detector and symbio app to further diagnose.
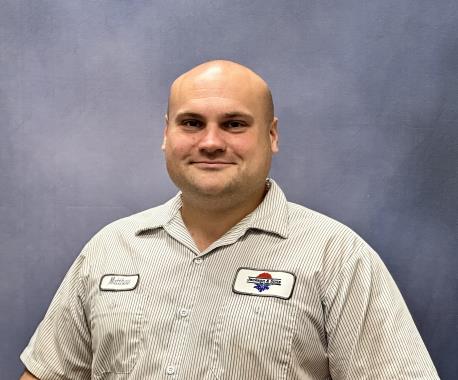
Matthew L.
.
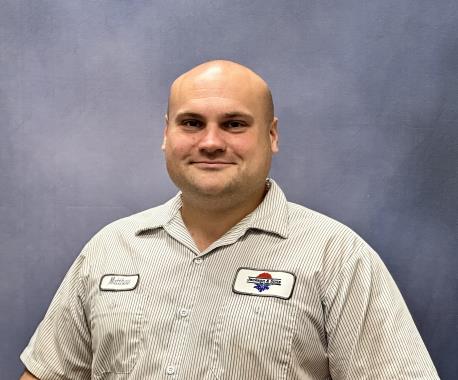
Matthew L.
Unit 2.1… checked wiring at air handler, condenser, and detector. All look correct. Could not pre test due to kids napping and no alert was sent to teachers. Need to return one morning to smoke test. Unit 427 is for room 427. Changed air handler fuses to 45 from 60. Changed fuses at condenser from 30 to 25. Unit for bathroom got pictures of air handler, condenser, and stat.
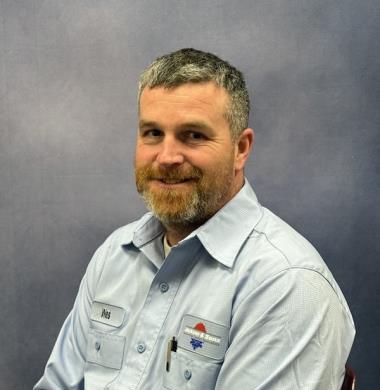
Wes B.
Package HP 5 - Right Side of store - upon arrival, blower door was off of the system. Tech replaced door for testing. technician found all electrical testing within spec. However, when checking the cooling, the technician found that the delta t was not sufficient. Temperature changeover was only about 11-12 degrees. Tech swept the indoor and outdoor coils with leak detector but the search came up negative. Previous notes on this system have stated there are some refrigerant challenges and this system has already been turned over to field supervisors office. System is capable of heating with assistance from heat strips. Package HP 4 - Middle of Store - appears to be new system installed in early 2024. No challenges found during today’s visit. System cleaned and inspected. System cooling and heating properly. Delta t on both heat and cool are between 19-22 degrees. Electric heat also tested and works to spec. Package HP 3 - Left Side of Store - upon arrival, tech found the system call
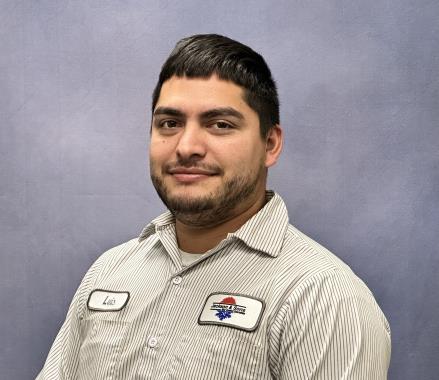
Luis R.
tech returned to replace auxiliary drain pan. Also, tenant noted water spots on ceiling. After investigation the tech discovered water was penetrating the roof and leaking onto ceiling. (Pictures provided).
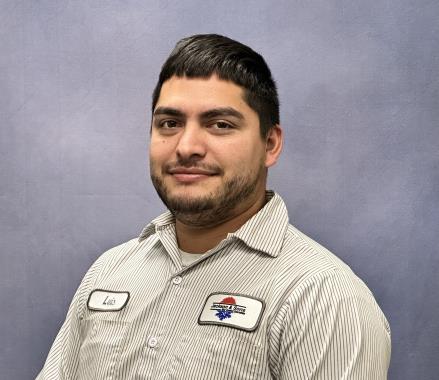
Luis R.
Techs replaced ther wire system is operating properly at this time.
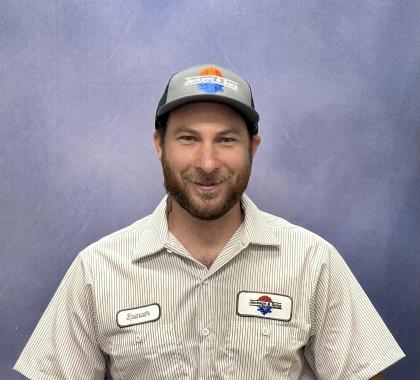
Spencer C.
Tech replaced constant torque blower and found normal operation. Customer also requested diagnosing school room 314 mini split. Tech added commercial service call fee. Tech found system running AC with a heat call. Mini split is ran off a Vision Pro connected to an adapter. Adapter has no O wire going to it therefore it cannot differentiate between a heat and cool call. Tech re wired and reprogrammed thermostat for a conventional system and found system running heat and AC modes. Adapter recognizes y for cool and w for heat and system runs accordingly. Tech also verified the heat pump runs in heat mode with a W call.
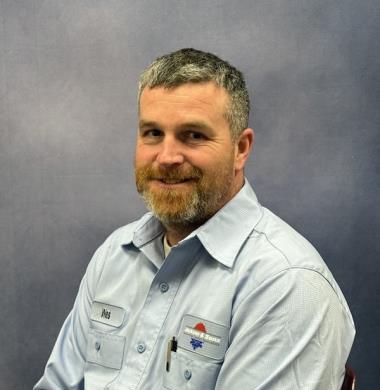
Wes B.
Performed CMA Inspection on 1 rooftop gas package unit, 1 split heat pump unit, 1 exhaust fan and 1 make up air unit. Gas pack - tech found no challenges with gas pack operation today. System is cooling properly and holding a 20 degree delta t. Tech also tested gas heat and found no challenges. Heat exchanger was inaccessible, however, the tech found no roll out or indicators of air infiltration at this time. Split Heat Pump - system is operating properly at the time of maintenance. The blower is emitting a squeaking noise as noted on last visit. Tech ensured belt is tight and aligned, however, the squealing persisted. As noted last visit, it could be due to the bearings on the blower shaft. Tech also tested function of exhaust fan and make up air unit. Make up air fan belt is loose and deteriorated. Will need to be replaced. Previous tech has built estimate for this repair. Filters - all filters changed and old ones disposed of.
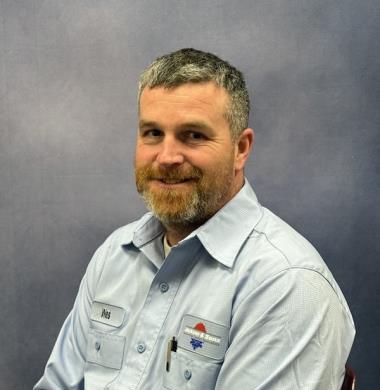
Wes B.
Performed CMA Inspection on 4 Split Heat Pump Systems. System 1 - technician did not find any challenges while servicing equipment today. The system is heating/cooling properly. Condensate lines flushed and re-primed. Tech also found the outdoor fan capacitor testing weak. Estimate built for this repair. System 2 - upon arrival the technician found the evaporator coil frozen completely. Tech verified blower operation and replaced filter. Tech thawed coil and performed leak search. Tech was able to find a leak. Office has been notified and is building estimate for repair. Tech also turned over to field supervisors office to give customer all options going forward. System 3 - per notes from last visit this system has challenges pertaining to the high voltage going to the air handler. Thermostat is blank at today’s visit, no voltage at the air handler. System 4 - no challenges found today. System is operating and cooling normally. Tech also tested heat and found no challenges. Attic
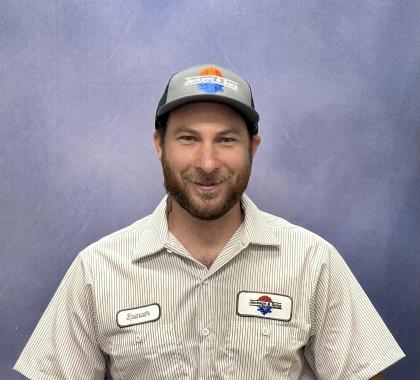
Spencer C.
Tech found a constant torque x13 blower rocking back and forth indicating a failed ECM. Customer approved repair.
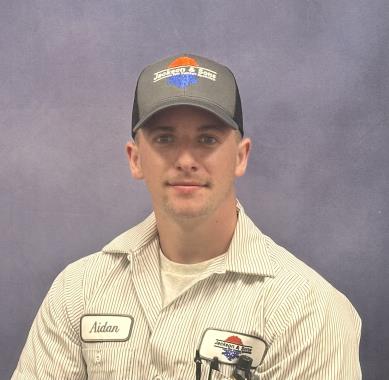
Aidan T.
- Tech replaced failed blower motor under warranty and confirmed proper operation. System is operating normally at this time. Thermostat set to 73 at tech departure.
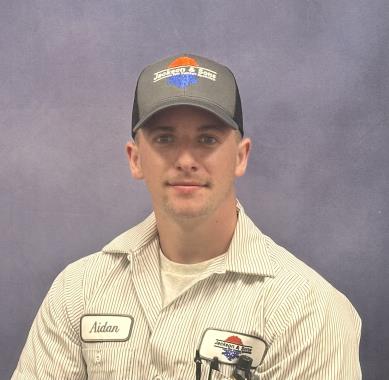
Aidan T.
-{Room 109 Packaged Heat Pump}- - Tech found hard lockout (4 flash) fault code displayed on the control board upon arrival. Cleared code and observed the blower motor not operating. Confirmed compressor and condenser fan are operational. - Confirmed 24v and 240v power input with no response from the motor. Blower motor has failed and must be replaced for system to operate. - Tech contacted office for pricing information; office will contact the customer with a repair estimate and schedule details. Left power off at disconnect to prevent further issues.
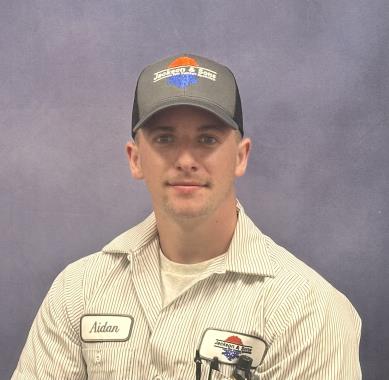
Aidan T.
- Tech returned and replaced zone board, transformer, and installed a resettable fuse breaker for testing. System tripped fuse breaker after restoring power. - Tech began troubleshooting for low voltage circuit issues and found upstairs thermostat was shorted on Y call. Checked wires and found no resistance issues; replaced upstairs thermostat and continued testing. Rewired entire upstairs wire configuration, rewired zone board 24V circuit and replaced contactor for testing. No issues observed with both thermostats calling for cool or each one individually. - Ensured proper programming on new thermostat, zone board, and removed testing contactor. - Replaced supply air temperature sensor and wiring harness connecting to zone board. Programmed 40°F low temperature cutoff and 140°F high temperature cutoff. - Confirmed proper fan speed on tap #7, original contactor ohm reading, and delta T measuring 19.7 upstairs and 18.3 downstairs. Tested both thermostats on heat mode and confirm
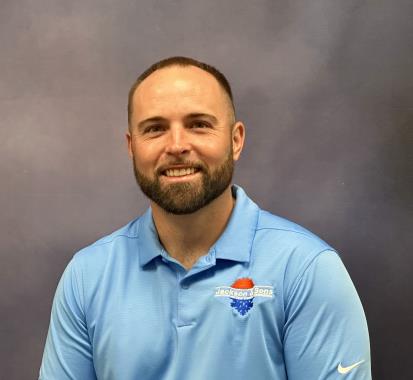
Aaron L.
CMA proposal
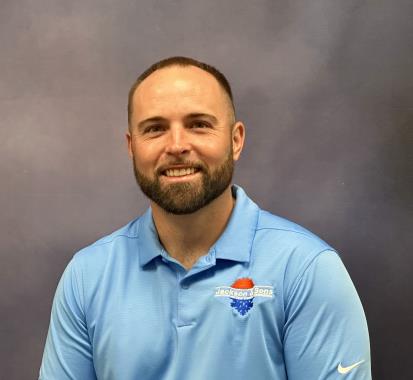
Aaron L.
Tools pictures and recorded information for a commercial maintenance plan
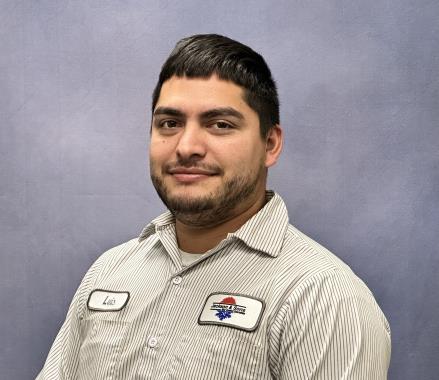
Luis R.
Technician found thermostat was shorting out when calling for y tech replaced thermostat for testing purposes and new thermostat still shorted out. Technician went up to roof and found no visible shorts or rubbing wires. Technician installed the thermostat wire on the units itself. Thermostat still shorted out. Technician replaced contactor and tested system thermostat was operating and system was operating properly. Technician rewired back existing thermostat and with new contactor thermostat still shorted out. Technician replaced wires at thermostat from y to pink and tested system still shorted out. Tech recommended replacing thermostat wire will require 2 techs due to being on 2nd floor and rtu is actually even to 2nd floor sitting on top of 1st floor roof. Will be very difficult to run.
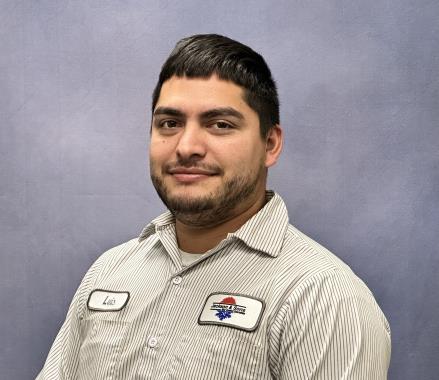
Luis R.
Technician found no power to smoke detector. Technician checked wiring on smoke detector found no challenges technician did see a splice down the line feeding the smoke detector. Tech inspected the splice found common wire was not wired in. Tech wired in the common wire to the smoke detector wire and s,one detector powered up.
Anthony B.
Replace 2 Ton Air Handler With New Trane 2 Ton Air Handler With WiFi Programmable Thermostat