Zebulon NC Heating Air & Conditioning Services
Jackson and Sons has been serving the heating and air conditioning needs of Zebulon, NC residents and businesses since 1974.
Our reviews below from your neighbors in Zebulon, NC tell the story of our quality, dedication and commitment to customer service.
Local Reviews
for Zebulon, NC
Customers say: The recent reviews exhibit a positive overall sentiment, with a slight inclination towards the positive. The reviewers express satisfaction with the services provided, highlighting the helpfulness, expertise, and professionalism of the technicians. They mention the timeliness, efficiency, and quality of the work done. Additionally, the reviewers appreciate the courteous and respectful behavior of the technicians, as well as their willingness to answer questions and provide detailed explanations. The positive reviews also mention the positive experiences with the company's customer service, including the ease of scheduling appointments, the clarity of the pricing, and the overall positive impression left by the technicians. However, it's worth noting that the negative reviews are fewer in number and do not contain any significant negative sentiment. Overall, the reviews suggest that customers have had positive experiences with Jackson and Sons and would recommend their services to others.
Our Reviews by City
Excellent experience
EVANS - Zebulon, NC 27597
Prompt, thorough,clean. Takes time to answer our questions, let us know how to prioritize future issues for planning purposes. Always polite, never tromp debris through the house. We have been happy customers for many years and plan to remain so.
Excellent same day service!
EVANS - Zebulon, NC 27597
There is never a good time for the heat pump to break but Jackson and Sons always is right on it, usually seeing us the same day and gets us back up and running quickly and professionally. We are long term customers and plan to remain so.
Great customer service
Heather - Zebulon, NC 27597

Chris A.
Tech washed and serivced unit, tech found no challenge at this time. Unit is operating properly holding a delta T of 20.
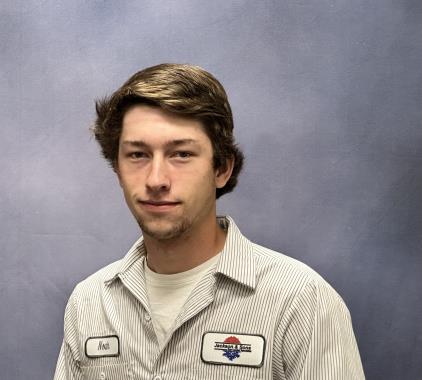
Noah C.
Upon arrival tech ran system in heat mode and found condenser to start up but blower did not start immediately. Blower started and system ran shortly before turning off and displaying error code F5. Found F5 to indicate shorted or open compressor discharge temp sensor. Ohmed sensor, according to 50k chart and Trane sensor is bad. Ambient sensor and coil sensor are also made into the same plug. Provided estimate to customer to replace. Customer will call with a decision tomorrow.
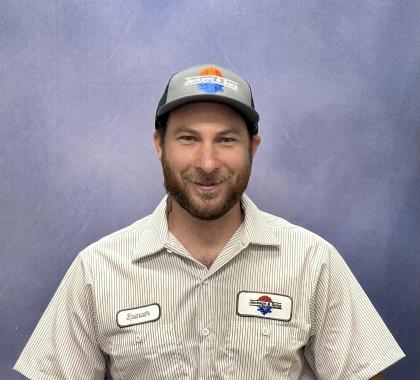
Spencer C.
Tech found blown low voltage fuse. Tech tested with a fuse popper and found fuse only blows on white circuit. Tech unplugged contactor and found fuse not blowing. Contactor has .3 ohms and is shorted. Tech also noticed water stains under the air handler and water damage inside airhandler. Tech recommends Maintenance plan to clear drains regularly. Tech replaced contactor and customer agreed to monthly ESA and system is now heating properly in heat and aux heat.
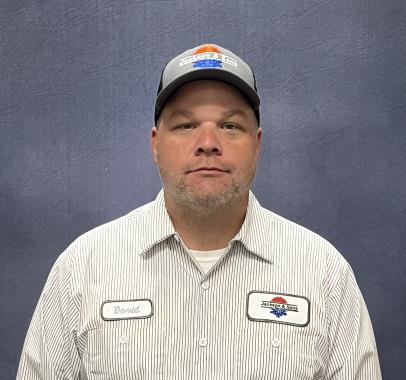
David S.
-Dropped off 1-14x25x1 & 1-20x20x1 air filter at inside garage door per instruction. Communicated with customer and verified garage door closed upon departure.
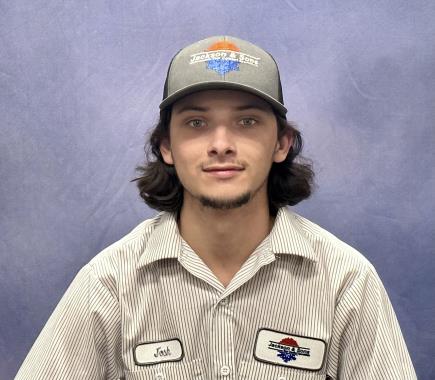
Josh W.
Tech perf Esa on two systems, tech did not find any issue with either system at todays visit. Both systems are back on and operating properly at this time. Will need to return with 14x25x1 and 20x20x1 filters. All is good at this time.
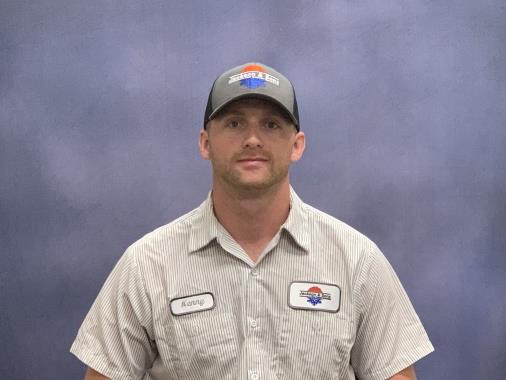
Kenny C.
Performed ESA, tech cleaned and serviced system. Tech found flame out of balance due to clogged burners. Did test rollout switch and switch tested within spec. System is back on and heating.
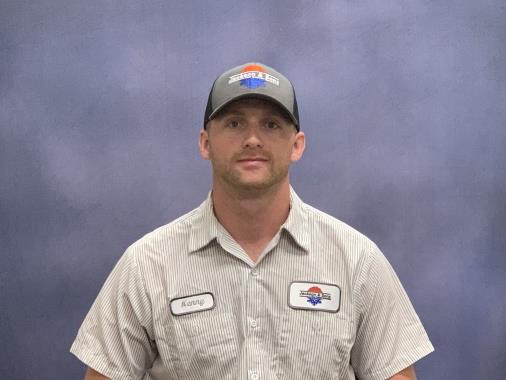
Kenny C.
Performed ESA, tech found no issues at todays visit. Homeowner extended ESA. Discussed plasma air purifier.

Kyle W.
Found dual run capacitor failed. Replaced under warranty pricing. System up and cooling. Customer also pointed out discoloration on hallway ceiling. Did not find any signs of condensation challenges from air handler. Verified proper drainage. Will need to keep a check on issue and double check during 1st maintenance. Invested in ESA (2) systems. Schedule 1st visit.
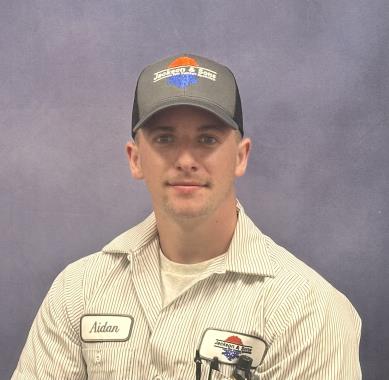
Aidan T.
Tech inspected and diagnosed HP units# 5, 6, 7, 10, 11, and 13. -HP #5 Faulty contactor not allowing power through. Replaced and system ran normally. -HP #6 System running normally. Advised installation of air filter. Pressures look good. Tech suspects unit 5 being down has forced unit 6 to carry both loads, decreasing efficiency. -HP #7 System running normally. Inspected electrical components and refrigerant pressures and found no issues. -HP #10 Not running efficiently. R22 compressor is likely losing compression potential. Pressures and amp draw look good. Management wants to replace this system. -HP #11 Compressor is shorting out. Runs for 3-5 seconds and smoke starts to appear at terminal plug-in before tripping the breaker. Capacitor read full capacitance. Management wants to replace this system. -HP #13 Condenser fan motor is seized. Receiving 230V power and capacitor is good. Overheats in 10-15 seconds before failing completely. Management wants to replace this system. Se
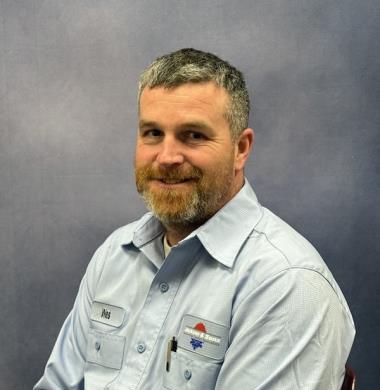
Wes B.
Performed CMA Full Service on 4 Rooftop Gas Pack Units, 2 make up air units, 2 condensers, and 1 DOAS system. Technician also ensured exhaust fans were operating during the time of maintenance. Challenge - GP 2 - technician observed circuit 1 not operating. There was a call for Y1 and Y2, however only circuit 2 was operating. Previous notes recommended a leak search of circuit 1 given that the system was likely low on refrigerant. Leak search performed and a leak was found in the evaporator coil of circuit 1 (video and picture provided). Office notified and a quote will be built with a goal to repair the leak. Challenge - GP 4 - upon arrival to the system the tech discovered that circuit 1 was not operating, similar to GP 2. Technician inspected system and found compressor to be reading GOOD, no challenges in terms of electrical. Tech then leak searched the evaporator coil and found a couple of leaks on the bottom portion of the coil (video and pictures provided). Coil is heavily rus
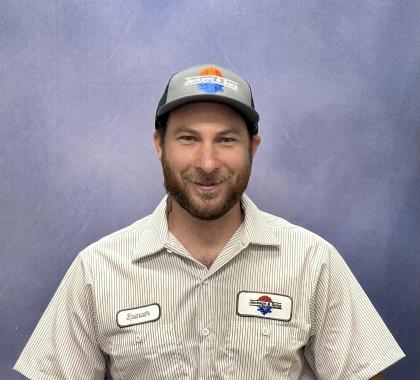
Spencer C.
Customer stated power outage and system was not cooling after. Customer stated system has been cooling since 8 last night and has not had an issue maintaining temperature. Tech offered to inspect system for system operational fee but stated it was likely due to power outage. Customer declined system operational and wants to see how system does. Tech instructed customer to call back if system is unable to keep up.
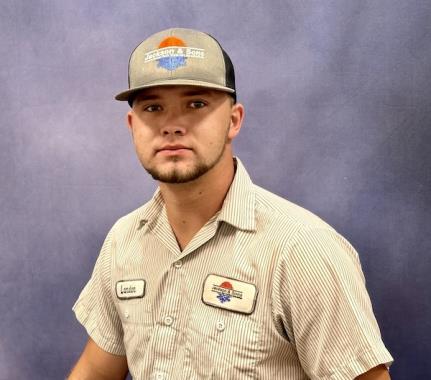
Landen H.
Tech washed and serviced unit and found condensate line to be clogged up and not allowing water to drain tech cleared line unit is draining properly at this time tech found no other challenges at this time. Unit ismup and cooling with a delta t of 23
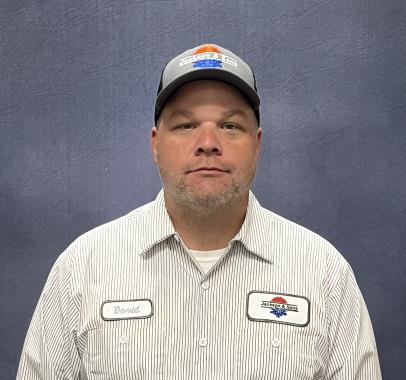
David S.
-Complete approved repairs as follows: -Replace 7.5 mfd blower motor capacitor on AHU-9. -Replace 5 mfd blower motor capacitor on AHU-15. -Replace 7.5 mfd outdoor fan motor capacitor on HP-5. -Replace 5 mfd outdoor fan motor capacitor on HP-8. -Replace 7.5 mfd outdoor fan motor capacitor on HP-16. Was improperly estimated as 5 mfd. -Replace 35/5 mfd dual run capacitor on HP-6. -Replace blower motor belt on Make Up Air Unit. -Approval to relocate thermostat on AHU-16. After discussing with installation field supervisor, deciding that adjustment on dampers to appropriate air flow at supply locations would be a better path for correcting temperature issues with various locations serviced by system. Did not relocate thermostat. Closed off damper to main hall bathroom to reduce supply air at that location.
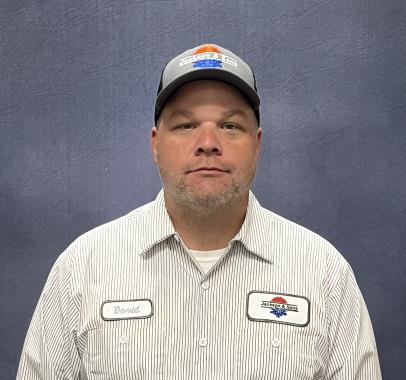
David S.
-Customer recently had a different company perform a service call on downstairs split system due to it not performing to his liking. That company informed him that refrigerant levels/pressures were low and that system needed R22 refrigerant added but they do not work with R22. -Customer is aware that low refrigerant levels are an indicator of a leak in system. Is aware that topping off is at best a temporary repair and that Jackson and Sons will not be responsible for length of time this charge may aid system operation. -Informed customer that system should be thoroughly inspected for any additional problems, and recommended maintenance options moving forward. -Customer wishes to proceed with top off only to system. R22 to be recharged to levels per pressure curves as shown on unit documentation. System currently cooling with temperature difference of 16 degrees.
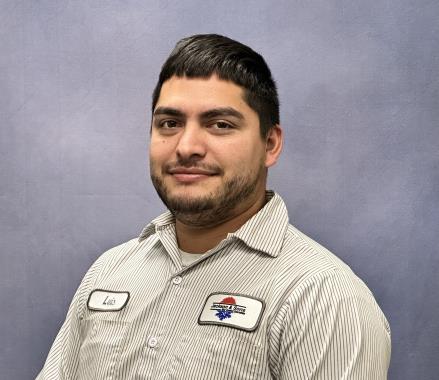
Luis R.
Tech pumped out water out of the auxiliary drain pan. Airhandler #2 is unleveled. Airhandler was leveled and cleared the drain line. Drain pan is corroded. Repairs for today are covered under install warranty.
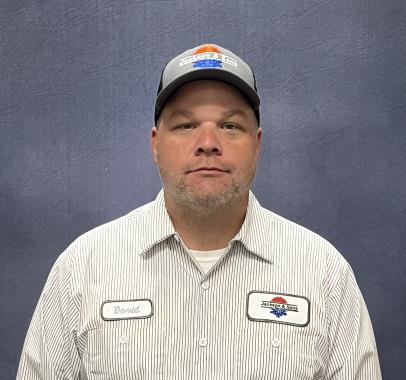
David S.
-Performed CMA Filter Change at 4 back of house locations, 1 DOAS System, and rooftop gas packs per maintenance agreement.
Anthony B.
X
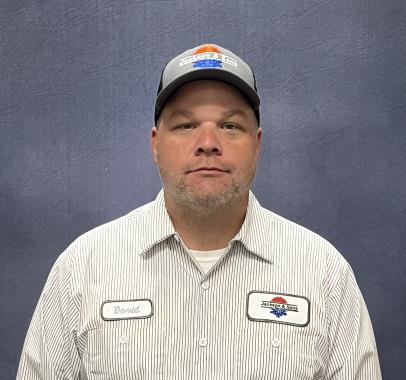
David S.
-Performed CMA Full Service on 16 Split System Heat Pumps. Verified operation of oven hood exhaust fan and make up air. Multiple repairs or recommendations for replacement of systems were made at last service in October 2023. Updated estimates provided. -System 2: Old style thermostat in place in hallway but no longer in use. -System 5: Outdoor fan motor capacitor tested weak and was recommended for replacement at last service. Provided updated estimate $217.59. -System 6: Outdoor fan motor capacitor & compressor capacitor tested weak and were recommended for replacement at last service. Provided updated estimate $322.61. -System 8: Outdoor fan motor capacitor tested weak and was recommended for replacement at last service. Provided updated estimate $213.00 -System 9: Air handler blower motor capacitor tested weak and was recommended for replacement at last service. Provided updated estimate $217.59. -System 10: Air handler blower motor capacitor tested weak and was recommended f
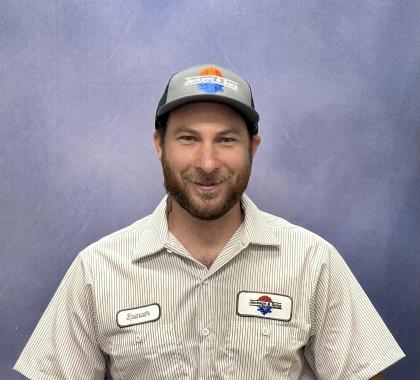
Spencer C.
Tech replaced and tested heat strip contactor and found heat strips working properly. Heat strips set off fire alarm and tech explained this was due to dust buildup on the heating elements from heat strips not running and assured no cause for concern.

Matt C.
Tech washed and serviced unit
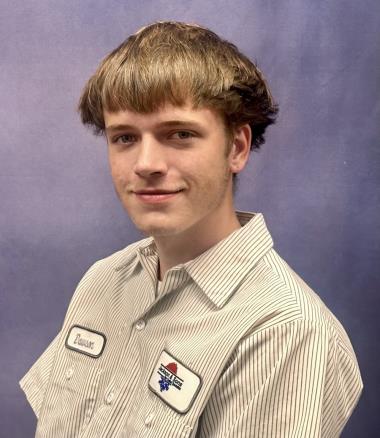
Dawson M.
Tech found no difficulties at this time. Homeowner extended Psa. Tech recommended plasma air.
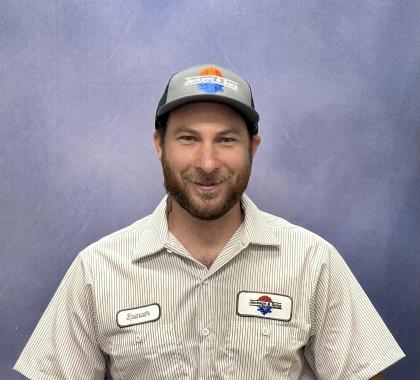
Spencer C.
Tech found thermostat constantly restarting and throwing insufficient voltage error. Heat strip contactor was shorted causing a voltage drop. Tech was told by Jeff to email estimate in order to get approval. Tech also found thermostat set to emergency heat. Tech removed the common wire from the limit switch connected to the contactor to allow system to run temporarily.
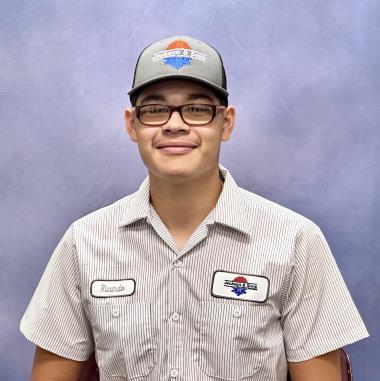
Ricardo T.
Tech performed ESA wanded coils no leaks at this time. Tech found dark pitted contactor tech suggested replacing sent estimate. Dropped off 20x30x1 filter.